USES OF POWDER METALLURGY IN RECENT DEVELOPMENTS IN VEHICLES
Updated: Nov 3, 2023
What is Power Metallurgy?
Powder metallurgy is a manufacturing process in which materials or components are produced from metal powders. It is a green technology (as it doesn't require melting metals or alloys which requires large amount of heat energy harnessed from Fossil fuels) for production of many shape components for example:
shock absorber, wipers etc
steering components
variable valve timing (VVT sprockets)
low valve seats in the chassis,
oil and pump components,
conduits, connecting rods, exhaust pipe bearing etc.
PM technology has the ability of mass production of reliable parts with precision and minute tolerance, consistently at a very cheap rate which is very attractive to the Automobile industry. PM provides particle design advantages such as uniformity in shape, design, flexibility applications etc. Moreover, such components are lightweight, high strength, easily customisable, and has a near net shape ability and low cost-performance ratio. At present average powder metallurgy products per vehicle in Europe is 14 Kg, in the United States is 19.5kg.

Powder Metallurgy Applications (image Credit: Woodhead Publishing Limited,2013)
Applications for PM abound and Metal Powder Industries Federation (MPIF) tracks new uses of PM and shares it with the manufacturing community.
STEPS IN PRODUCTION OF POWDER METALLURGY PRODUCTS
The process of manufacturing has the following steps:
1. Generation of powder
The size of powder affects the properties of the parts to be made. Some ways to generate powder are:
A. Mechanical Process
By Machining, Crushing, Atomization
B. Physical Process
By Condensation, Thermal decomposition
2. Blending or mixing
Powders are to be blended properly for achieving the required properties. A lubricant is used for reducing friction and obtaining better mix. Although it should be removed before the next step so that required properties should be obtained.
3. Compacting
Compacting is done for shaping of powder to get the desired shape. Shape has no restrictions as powder can take up any shape. It is done by applying pressure so that gap between molecules is reduced and it gains required strength Processes applied are:
Isostatic Pressing; Vibratory compacting
4. Sintering
This process is done to increase strength and also hardness of the part. The part is subjected to heating without applying any pressure for some time under controlled conditions. Sintering is concerned with diffusion, densification and recrystallisation and rain growth.
3. Sizing (or Impregnation)
After the above process the produced part is compared with the masterpiece. Pressure is applied on the part so that the pores and other gaps get closed and it becomes impossible for oil or water to occupy that vacant space.
4. Testing and Inspection
Several tests are applied before it is put in use, for example- test to check compressive strength, tensile strength, porosity, hardness etc.
Various parameters on which the quality of powder metallurgy products depends are:
Size and shape of particles
Distribution, density, porosity, chemical composition, and surface characteristics of particles.
Sintering time, temperature and pressure applied
All above can be controlled during the manufacturing process. Thus, powder metallurgy provides us immense freedom to control the properties of its products.

Fundamental Processes of Powder Metallurgy
BROAD APPLICATIONS OF POWDER METALLURGY
Powder metallurgy has been used in industries since the 1950's. It got a real boost due to increasing environmental concerns, reducing fuel consumptions, developing lightweight technologies, and engine downsizing for environment friendly vehicles. It has generally been used in two major fields- ferrous precision parts and hard metals, 90% of whose products are used in the automobile sector. Today the main products are:
Structural Parts
The main products are iron alloys. Consistent efforts are made to improve their properties and suit them for specific tailor-made purposes such as agricultural machinery, automobile parts . Pulleys, valves ,drivetrains, valve control systems made with such materials help to improve fuel efficiency by over 1.5 times. PM products support acceleration in greening of technology, transition to hybrid electric vehicles, making parts thinner and lighter at the same time maintaining strength, precision at lower production costs. Chromium is often used in sintering process for strengthening parts.
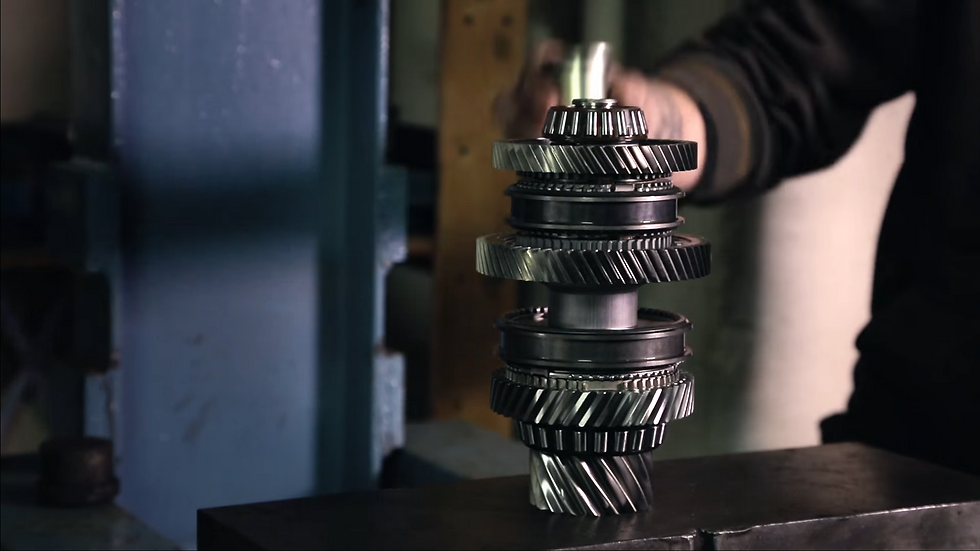
Tribological Parts: The parts that are strongly exposed to abrasion and lubrication. In his field PM alloy products and microstructure are used. Such products can easily bear oil, high temperature, and are wear-tear resistant. Use of such products reduces servicing cost of vehicles. Recent advancements can support high pressure and temperature that can withstand high temperature in turbo-chargers and helps to reduce its size and weight.
Magnetic Parts: To support ICT(information and Communication Technology) equipment, soft magnetic materials are required. Today ICT equipment continues to be faster, use higher frequencies, become smaller, and use less energy. So new sintered magnetic materials are developed consisting of structural and magnetic materials, powder cores(or SMC soft magnetic core) that support low core loss in high frequency regions.
Next Generation High Performance Parts: Powdered metallurgy is increasing its applications in new fields such as information home appliances, environmental energy sources and life sciences for developing compacting micro parts that are difficult to build traditionally through machining and metal injection moulding (MIM).
POWDER METALLURGY PARTS USED IN VEHICLES:
1) VVT powder metallurgy parts: VVT or VCT(Variable Cam Timing System) helps to enhance engine output. We know that valves help in intake and exhaust of air mixtures in engines. The timing of air intake and exhaust is controlled by the shape and phase of the camshaft. At different speeds the duration of intake and exhaust is different, and so the speed of camshafts needs to change accordingly. At higher speeds intake and exhaust durations become very less and so the engines fail to get sufficient air. So the exhaust and intake valves need to overlap. It improves speed and fuel economy.

In 1980, Alfa Romeo first used VVT technology, Honda used it first in 1989. In such variable pumps Powder metallurgy products perform better than traditional counterparts.
2) Oil pumps: Engine oil pump and automatic transmission oil pump and automatic transmission oil pumps use an internal cycloid shape pump and external rotors. These parts are made from 75-78 parts of Fe powder, 7.5-7.8 part of Ni, 0.5-0.8 part of graphite powder, 3.1 to 3.4 parts of Cu, 9.2 to 9.6 of Mo,0.3-0.5 part of MgS, 2.5-2.8 parts of paraffin, 8.3-8.7 parts of Cr, 0.4-0.6 part of Sb, 1.3-1.4 parts of Bi, 3.2-3.4 parts of Ti and 2-3 parts of auxiliaries. Since the alloy powder is evenly scattered, the fatigue life is increased, has high strength, high impact toughness and good abrasion resistance.

3) Powder metallurgy products in Brake Booster Vacuum Pump: Most vehicles with petrol engines use vacuum created by the engines in the intake manifold to boost the response of the braking system. To meet the emission and environmental protection requirements, petrol cannot be used directly for the same purpose. So a pump needs to be installed. In diesel engines, the same amount of vacuum cannot be generated, so a pump is needed there also. The pump derives its power directly from the engine. The power drives the powder metallurgy made rotor and then the plastic valve. The rotation of the valve creates vacuum and braking action is assisted.
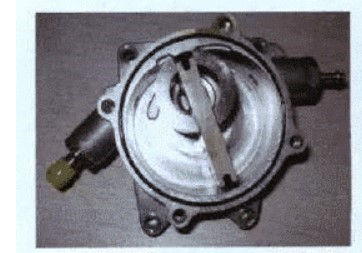

4) Powder metallurgy in helical Gears: Powder metallurgy is a proven technology to make high strength gears. These gears are less costly than a gear made of iron or steel. Less energy is required in its manufacture and there is too little waste materials. They require very little machine finishing. The porous composition makes it lightweight, and runs with less noise. These gears can be impregnated with oil resulting in self lubrication. But these parts have a drawback too. The powdered metal is not as strong as steel, and wears down quickly. These should be produced in large quantities to be cost effective.

5) Powder Metallurgy in Engines: Powder metallurgy products help to reduce fuel consumption and increase performance of engines. Powder metallurgy has played an important role in development of new engines by making better components and by improving possibilities in newly developed systems. PM has also helped to reduce costs.
Camshafts, traditionally, were made of solid bars. Today, PM technology allows us to use intermediate rings on a hollow tube helping in better precision, wear resistance and less weight.

6) Powder Metallurgy in Connecting rods: Powder forged connecting rods have higher tolerances. Splitting a single structure into several rods has resulted in better improved balance.

7) Other Applications:
a) Soft PM magnets are used in making fuel injectors which result in less fuel consumption and emissions.
b) In Exhaust Gas Recirculation Systems (EGR) the valves and actuators work at high temperature in an environment containing hot gases. PM parts have better performance in terms of durability.
c) Passenger cars with front wheel drive and rack and pinion steering mechanism (like Maruti) have a PM steel bulkhead assembly.
d) Shock absorbers like piston cylinder ends, compression valves can also be made using PM technology.
MATERIALS USED IN POWDER METALLURGY:
A variety of metals are used depending on needs and applications. Some are described here:
In ferrous category Fe, Fe-Co, Fe-Cu, Fe-Cu-C etc, are used for structural parts like camshafts, connecting rods, oil pumps etc. Mo, Ni, Si, Cu are expensive and so they are being replaced with Cr, Mn, Si.
For wear-tear resistance like valves, brake parts Fe–Cr–Mo–W–V–C, Fe–Cu–Sn–P–C etc are generally used.
Aluminum parts help to reduce weight and increase fuel efficiency of the vehicle. For shaft bearing caps, oil pump rotors, shock absorbers Al–Si, Al–Cu–Mg, Al–Zn–Mg–Cu, are used.
Better properties can be achieved through rapid solidification of the powders and then using hot pressing, forging or hot pressing to form parts like cylinder liners, rotors for automotive air conditioners.
Titanium is used for applications such as inlet valves, fuel pump filters, screws and nuts etc.. Using PM titanium in power train components helps to reduce the weight in reciprocating applications. Moreover, it can be produced at lower cost than conventional titanium route.
Nanomaterials have shown improved mechanical, electrical, optical, chemical, magnetic and electronic properties and are used in energy conversion, pollution reduction, sensors etc.
ADVANTAGES OF POWDERED METALLURGY OVER CONVENTIONAL METHODS
Dimension Precision: Powder metallurgy
Quality
Design Flexibility
Affordability
Strength
Speed
Scrap Efficiency
CONCLUSION
Powder metallurgy is a manufacturing process for economical mass production of precision components using different types of materials. It is attracting the attention of the automotive industry. Many developments in PM applications have emerged from cooperation of automotive designers with materials, manufacturing and value engineers.
The automotive industry has undergone considerable changes in terms of performance, reduced fuel consumption and environmental effects and improved safety. PM has helped here by improving existing components and by allowing the introduction of innovative components. The introduction of eco-cars could be seen as a threat, but is providing opportunities for the use of PM in the development of new products in the areas of functional electromagnetic controls and drives.
LIMITATIONS
Products must be manufactured in large quantities for the process to be economical.
Sometimes the density of different parts of the final product can vary due to uneven compression.
Mechanical properties of the parts are of low quality as compared to cast or machined parts.
There is a lack of knowledge about this new technology, missing data on properties, shortage of trained personnel in this field. There is a lack of accepted guidelines about this new technology.
Gradual introduction of electric vehicles is a threat to the PM industry because these products can only be used in IC engines.
REFERENCES
https://www.pm-review.com/articles/powder-metallurgy-products-in-fuel-efficient-and-environmentally-friendly-vehicles/
https://cataluscorp.com/powder-metallurgy/auto-parts/
https://fdocuments.in/document/advances-in-powder-metallurgy-automotive-applications-of-powder-metallurgy.html
https://www.meetyoucarbide.com/application-of-powder-metallurgy-in-automobiles/
Automotive applications of powder metallurgy P. Ramakrishnan, Indian Institute of Technology Bombay, India
https://en.wikipedia.org/wiki/Powder_metallurgy
https://www.mc.showadenko.com/english/report/054/54.pdf#page=12
https://www.horizontechnology.biz/blog/powder-metallurgy-vs-machining-advantages-disadvantages
Powder Metallurgy Progress, Vol.18 (2018), No.2
Materials Weekly 22 May 2019
Commentaires